Crossdocking
Definition
Crossdocking is a form of distribution. With this form of distribution, incoming goods in a distribution center are shipped almost immediately after unloading. The goods are not first stored in a warehouse in between.
Crossdocking often takes place in large rectangular warehouses. Goods are unloaded on one side and loaded again on the other side for departure.
Activation
For cross-docking a module license is needed. To activate the license, go to Administration > Setup > WarehousePro Settings > License > Module Licenses. Also, a user needs to be connected.
After restarting the addon Crossdocking functionality can be activated via Administration > Setup > WarehousePro Settings > Crossdocking.
Process
Relation Sales order <> Purchase order
The cross-dock process is activated when a relationship has been established between the acquisition document and the customer order based on a (WarehousePro) allocation.
When creating an acquisition document, enable the setting via Administration > Setup > WarehousePro Settings > Crossdocking, to automatically create an allocation on a purchase order.
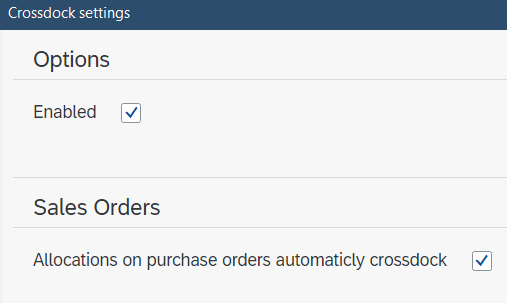
When Allocating on purchase orders automatically crossdock is enabled, allocated purchase orders will be automatically crossdocked.
If acquisition documents are not used, for example in the case of Material Resource Planning (MRP), allocations can still be added in the following way:
Manual: Allocations can be made manually from the customer order, see pictures below. In this case, the crossdock from the allocation of the purchase order can be manual enabled at the purchase order allocation screen.
Automatic: With an allocation profile, allocations can be made automatically.
See also the allocation part of this manual.Stock Allocations
Sorting Sales orders
WarehousePro will determine the order in which customer orders are eligible for the cross-dock process based on a certain sorting.
Suppose there is one order with ten pieces of item A.
Related to this order are four customer orders with a total of ten pieces of item A.
When physical goods are received, it appears that only six pieces of the ten are present.
In such cases it must be known which customer order can be processed first. The standard fields used for this are (in this order):
Delivery date (line level) > For multiple lines with the same item, the delivery date at line level is leading.
Posting date (document level)
Posting time (document level)
The output is visible in a crossdock report, which can be consulted via WarehousePro > Reports > Crossdock Report

The crossdock report is based on real-time. information.
Creating crossdocking locations
Crossdocking locations can be added via Administration > Setup > WarehousePro Settings > License > Crossdocking > Crossdocking locations.
Crossdocking Goods Receipt Client
The first step when receiving goods is selecting/scanning the item (Goods Receipt - Lines). After selecting/scanning an item, WarehousePro will assess whether there is a purchasing allocation for this item.
After selecting the line with crossdock you will arrive at the "crossdock order information" screen.
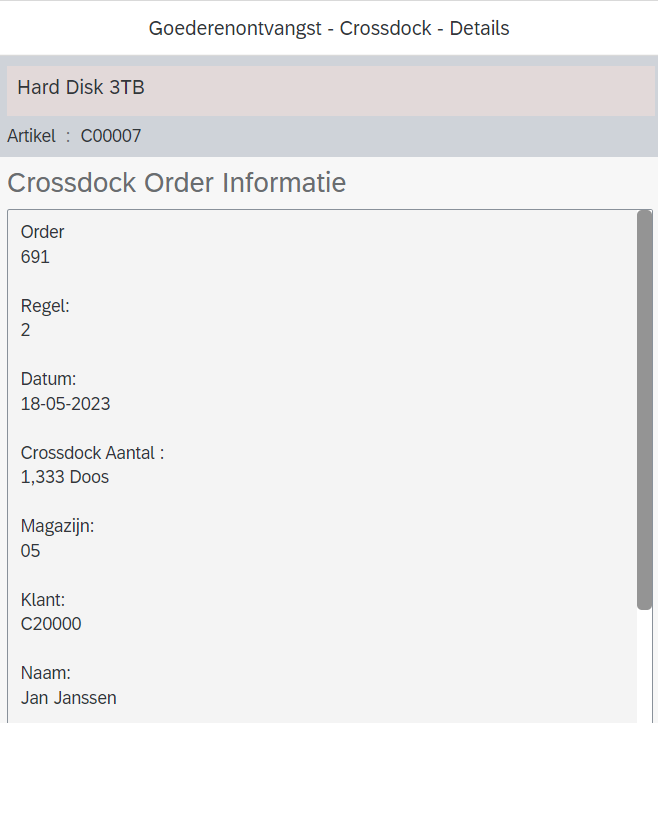
This screen can be adjusted using "Details Definitions" event "XDock_Order_Details".
Crossdocking handling is NOT supported in EDI goods receipts.
Starting crossdocking
The first screen in this process is Goods Receipt - Crossdock - Location. This screen shows information about the customer order and the required quantity. The warehouse employee must scan a warehouse location that is characterized as a cross-dock location. Created Crossdock locations are recorded in WarehousePro, possibly in combination with a location attribute.
The next screen in the Crossdock process is also a new screen: Goods Receipt - Crossdock - Quantity. This screen again contains information about the customer order and the required quantity. This screen is repeated per order line containing allocations.
Suppose you have received a total of ten pieces, containing two allocations of four pieces.
You will first see the information of the customer order with the highest priority (see Sorting Customer Orders).
Then the second customer order, and finally the two remaining pieces for stock, based upon setting “Crossdock Priority”.
After specifying the quantity, the item has been received. When there are more items in the order, the Client will return to the Goods Receipt - Lines screen.
If this was the last item, WarehousePro will post a Goods Receipt in SAP Business One. At this point, the allocation is converted to an inventory allocation.
Crossdock customer order
An inventory allocation does not ensure that the stock at the cross-dock location is actually reserved for the corresponding customer order. A picking list is required for this. The most obvious option is to generate this picking list automatically via WarehousePro. A separate order picking strategy can be used in the profile. Only the cross-dock locations can be included in the strategy and a priority can be worked on if necessary.
Picklists are recognized to Create User. In the Database, a field is added “FromCrossDock“ to table “APD_OPKL“. After goods receipt a picklist will be generated.
In goods receipt screen a tab Crossdock has been added. This is also shown in the generated picklist.
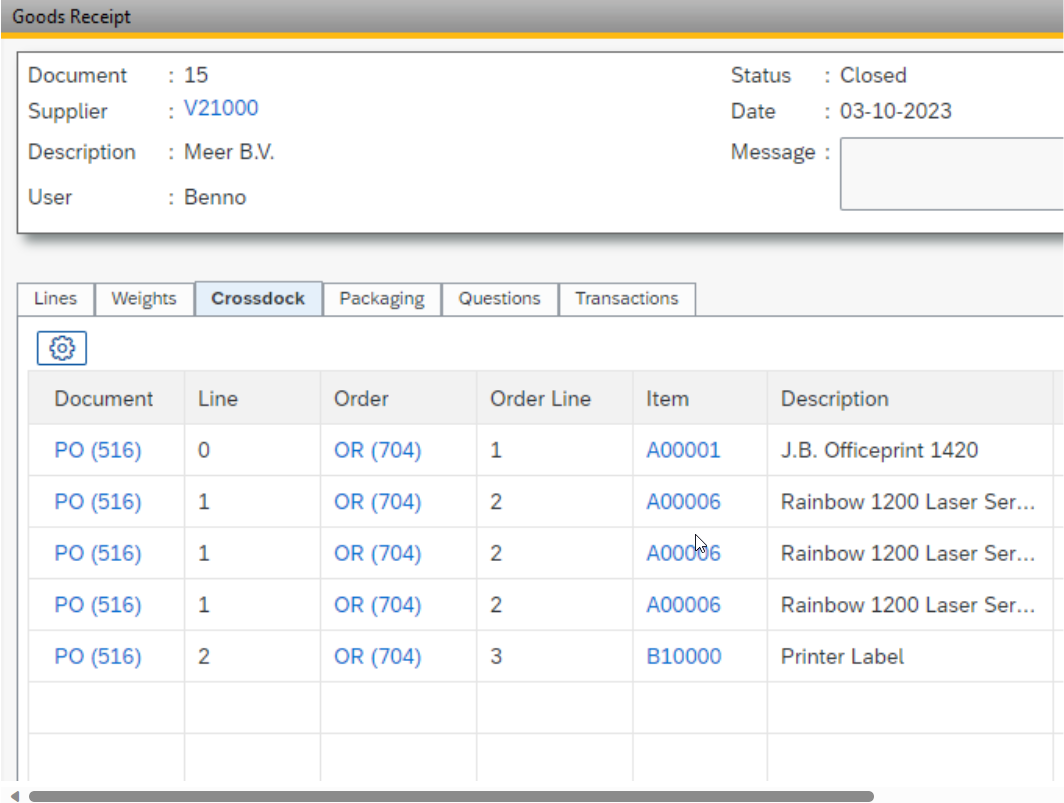
In a crossdock picklist allocations are added (this differs from normal batch/serial numbers) when the receipt document is manually transferred to SBO (i.e. outside WHP).
Crossdock reservations for which there is no WarehousePro goods receipt document are then converted to stock allocations.
Picklist settings
For crossdocking, you can set up specific picklist settings for Sales orders and Reserve Invoices.
Use default
When the 'Use Default' option is checked, the picklist settings configured in WarehousePro Settings > Picklists > Settings will be applied. This means that the picklist settings set up in the crossdock section will no longer be valid.
Any invalid settings will be greyed out. This also applies to any expedite locations entered
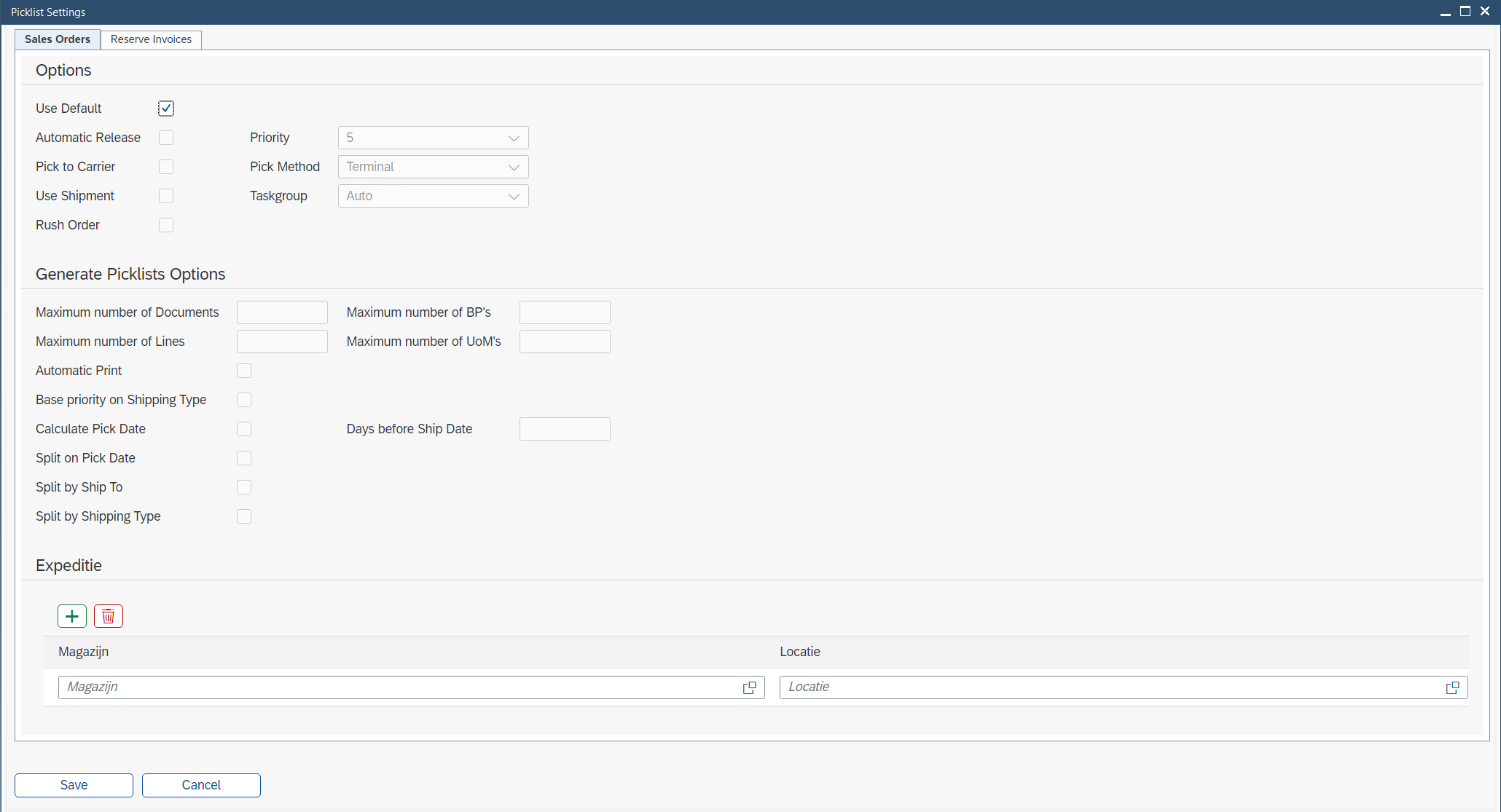