Stock Allocations
Introduction
WarehousePro contains possibilities to allocate existing, not yet received or not yet produced stock to sales or production orders. It is also possible to do this without the intervention of employees. There are various options for triggers on which allocation must be started.
The functionalities described in this document are available from version 3.1.2.7.
Settings
The WarehousePro SAP Business One addon contains a separate menu for the settings for allocating inventory. These settings can be determined via the menu path: Administration> Setup> WarehousePro Settings> Allocations .
General Allocation settings
Via the Settings menu option, within the above-mentioned menu path, general settings for making allocations can be specified per document type. Specific options are available per document type.
Brief explanation of all available parameters. Per document type (Sales Orders, Reserve Invoices, Production Orders and/or Request Stock Transfers) it can be determined which options should be available.
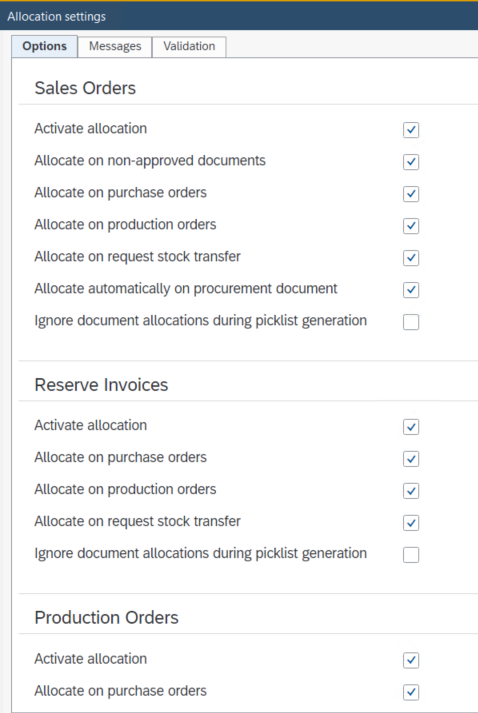
Options
The following options are available for document types Sales Order, Reserve Invoice, Production Order and Stock Transfer Request.
Activate allocation This parameter determines whether the allocation options for the document type become available.
Allocate on non-approved documents (only applicable to sales orders) Determines whether it will be possible to allocate on documents that do not yet have the Approved mark.
Allocate on purchase orders This makes allocation on open purchase orders possible.
Allocate on production orders This makes allocation on open production orders possible.
Allocate on request stock transfer This makes allocation on stock transfers requests possible.
Allocate automatically on procurement document Makes it possible when a procurement document (purchase or production order) is generated from a sales order, to automatically allocate the required quantities on this document.
Ignore document allocations during picklist generation When active, allocations on (Purchase Order, Production Order or Stock Transfer Request) documents are ignored when creating pick lists when there is free available stock. The allocation on these documents will be removed after generating the pick list.
Messages
It is possible to enable or disable whether notifications should appear when opening a document that has a pick list or allocation. This message appears in the message bar of SAP Business One.

Validation
It is possible to validate the editing of documents on which allocations are present before changes are made. A distinction can be made between checking at line level or a final check on the entire document. The combination of both is also possible.
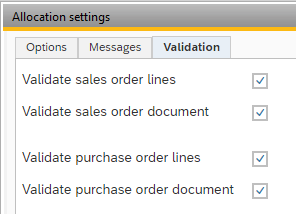
Allocation Profiles
Profiles can be created to generate allocations. A profile can be used to determine what the trigger is, which filters are used and which options should be used to determine how the allocation should be determined. Multiple profiles can be active alongside each other. Separate profiles must be created for each target document type (for which the stock must be allocated).
A profile can be deactivated if necessary.
Event type
A profile for Allocation can be determined on different "triggers":
None The profile is not executed automatically. Can be used when creating allocations manually.
Event An SAP Business One document (Sales Order, Reserve Invoice or Production Order) is added or updated. At that time, the allocation must be generated. This profile is only executed in those cases and will no longer attempt to generate an allocation again at a later time. An event will always be based on one specific SAP Business One document.
Interval At a specific Generation time or between a Start and an End time this profile will be executed and it will be checked whether documents or lines of documents are valid for this profile.
Event and Interval This profile is used when creating or updating an SAP Business One document as well as at a specific Generation time or between the indicated Start and End time. This type can be used when the allocation must be created immediately. If this was not successful at the time of creating or updating the document (because stock or documents were not available at that time), the interval will automatically check again.
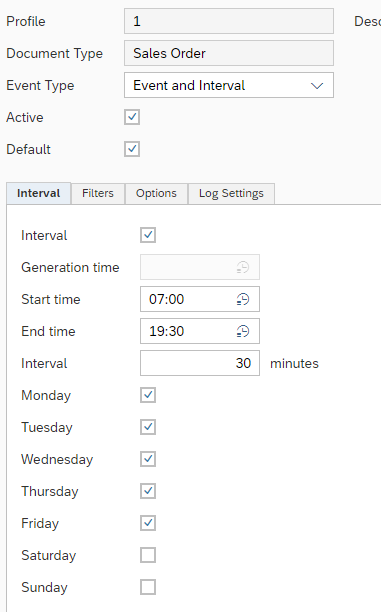
Interval
The Interval of a profile can be set in two ways: Interval between a start and an end time or at a specific Generation time. In both cases, it is still possible to specify on which days of the week this profile must be executed. If an Interval is chosen, the smallest interval of 10 minutes applies. This is to prevent heavy queries from constantly overlapping each other.
Filters
The Filters can be fixed in a profile. These are the same standard filters in combination with a possible additional SQL Filter.
The value 0 for the Days before date and after filters represents the current date.
Options
Under the Options tab you can determine how the allocation is to be determined. The tab consists of blocks which represent the source of stock that can be checked. Bear in mind that a source must be active in the general settings to be able to actually use it.
Each block contains 2 fixed settings:
Allow Allocation Determines whether on this source of stock are checked for available quantities.
Sort Order Determine which source should be checked first and which next. Each block must contain a unique value.
A few specific settings are possible for each document source (purchase or production order):
Prefer single document If active, the required quantity will be allocated on one single document.
Allow divided allocations (only active with Prefer single document) If the required quantity could not be allocated from one single document, a second run is done in which the numbers can be divided over several documents.
Cross Dock (only active when Cross Docking function is enabled) Enable if the required quantity should be reserved with Cross Docking options to prevent the new inventory to be stored in bin locations.
Two variants are available per document source (purchase or production order):
Before date Document lines with a receipt date (or production date) beforethe delivery date of the target document line are checked.
After date Document lines with a receipt date (or production date) after the delivery date of the target document line are checked.
In addition, it can be indicated how the required quantity should be handled. For each source the choice can be made from one of the available options.
Available quantity The available quantity will be allocated. No account is taken of any sales or packaging units.
Full document UoM The required number is allocated according to a multiple of the unit used in the target document (sales order, reserve invoice or production order). If the base unit was not used here, a multiple of the contents of the unit used are allocated.
Full sales UoM The required quantity is allocated according to a multiple of the Sales UoM. Regardless of what the unit used in the target document (sales order, reserve invoice or production order) is.
Full purchase UoM (Only available onsource type Purchase) The required quantity is allocated according to a multiple of the Purchase UoM. Regardless of what the unit used in the target document (sales order, reserve invoice or production order) is.

Depending on licenses, the Production related block might not be visible.
Log Settings
Under the Log Settings tab, you can specify how many days logging about allocating inventory based on this profile should be saved.
This logging can be requested via the Log button at the bottom of the screen:
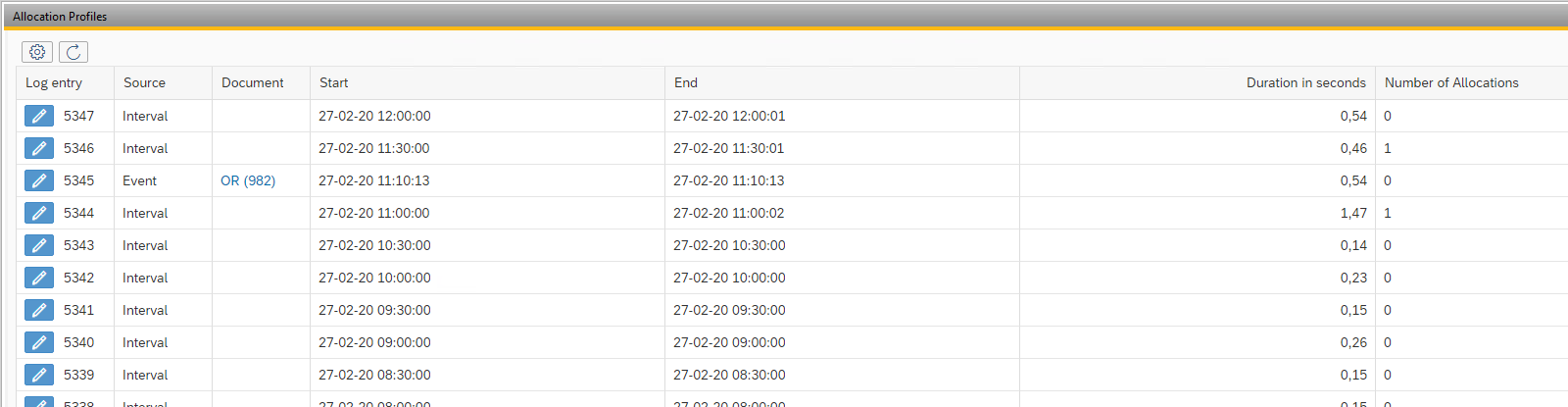
If necessary, the profile can be started manually via the Execute button (not available for Event type None).
Allocate Stock
WarehousePro contains various options for allocating on existing stock or on open purchase or production documents. This ranges from a simple right-click function to fully automatic allocation of numbers without user intervention.

As soon as a pick list is generated, the allocation is transferred to a hard stock reservation.
If this pick list is canceled, the stock allocation must be made again.
Manual Allocation
From the SAP Business One document (for example the sales or production order) the allocation screen can be opened via the right mouse click menu via the option WarehousePro Allocations for order.
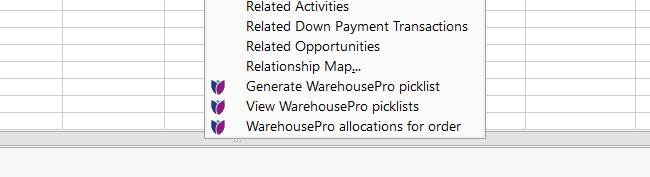
A screen appears in which the open order lines are displayed. This screen contains separate columns for allocation on stock (Assigned), Orders and Production orders. In the column Assigned, you can easily enter the number that must be allocated.
By clicking on the icon in the Orders or Production Orders column, a screen appears with available document lines where the number to be allocated can be specified in the Assigned column.
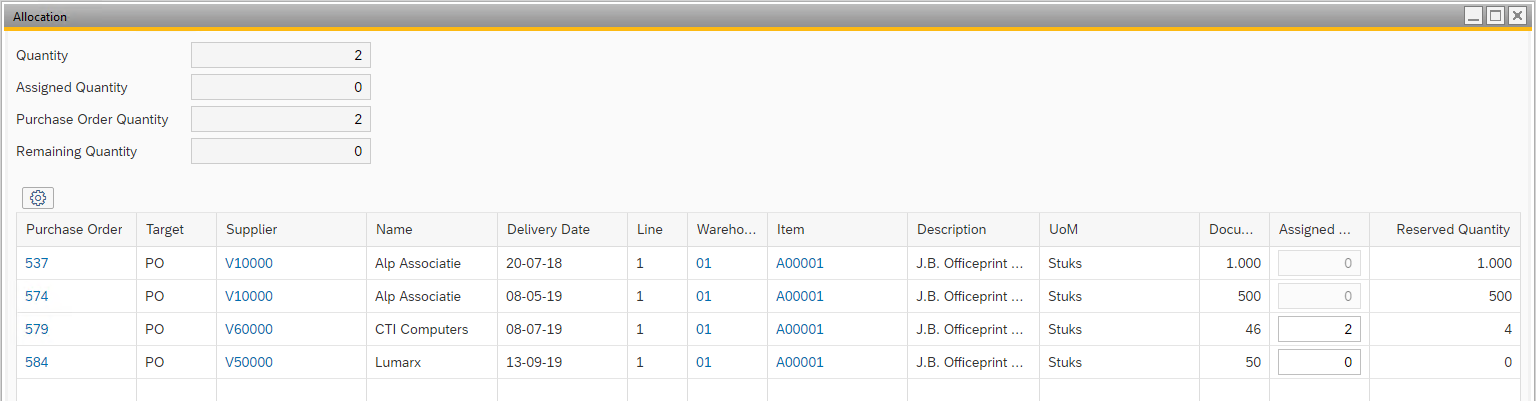
For stock and document allocations, it applies that when the free numbers are no longer available, then the input fields are blocked.
The Reserved column shows the total quantity that is allocated minus the quantity for the document that is allocated to. In the example from the screen print above, the total number allocated to purchase order 579 is actually 6.2 for this order and 4 for another document.
At the bottom of the screen for manual allocation there is also a button Allocate all. When this button is used, the selected profile (to be selected at the top of the allocation screen) will also be used to assign all unfilled allocations where possible.
Automatic Allocation
It is also possible to have the allocation generated automatically. By setting up profiles, this can be done completely in the background based on events in SAP Business One or at specific times during the day.
Allocation locations
Use this function to exclude locations from allocation.
For example: goods that are at a receiving location (Put Away) or quarantine location. These locations may not be used in the allocation process.
In the entry screen all Warehouses, area's, bin locations that filled in are defined as allocation locations. While generating pick lists or checking SAP documents (deliveries, etc.), it is checked at warehouse level whether there is sufficient stock.
It is possible to work with specific characteristics of bin locations when using Attributes on top op the entry screen.